PVD Processing
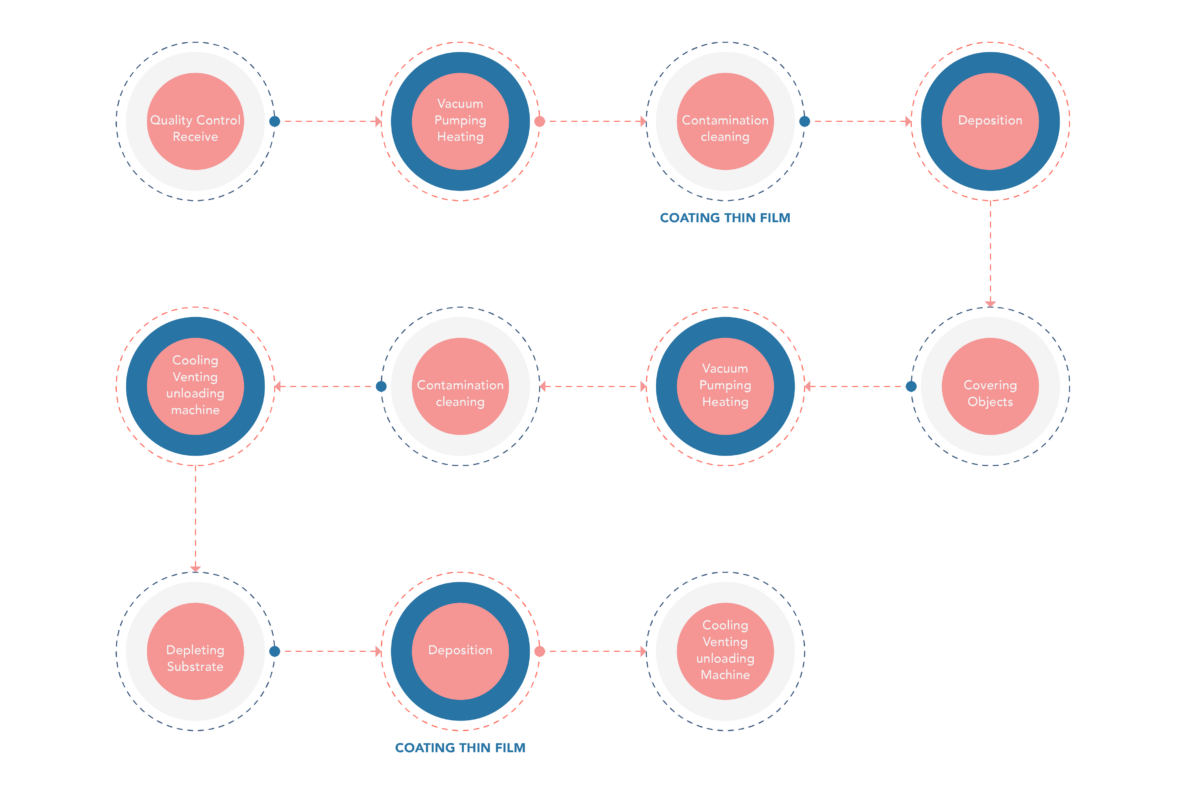
Here Are the Three Main Types of PVD Coating
1. Thermal Evaporation There are two types of thermal evaporation:
Pulsed laser deposition and electron beam deposition. Both processes use energy to evaporate a metal material (such as Titanium, Zirconium, Chromium, Aluminum, or Copper) into a vacuum. The vacuum then allows vapor articles to travel to the relatively cooler production parts where it will once again condense and crystallize into a thin, hardened, metal state. This PVD type is most commonly used in computer industry microfabrication or for products such as film packaging.
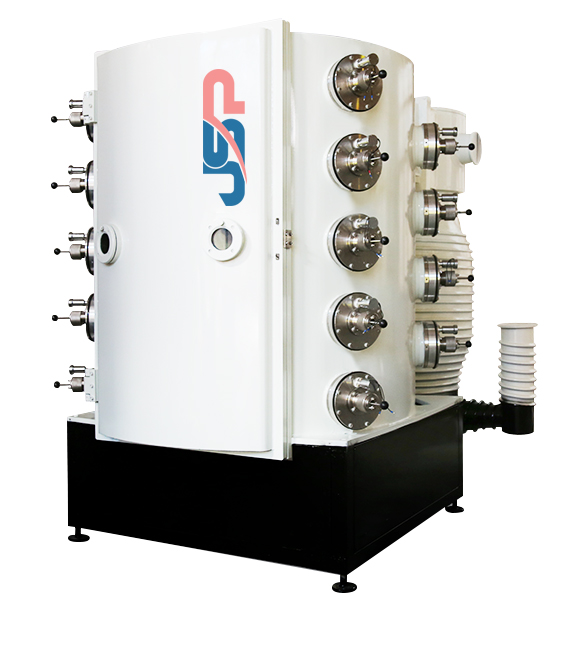
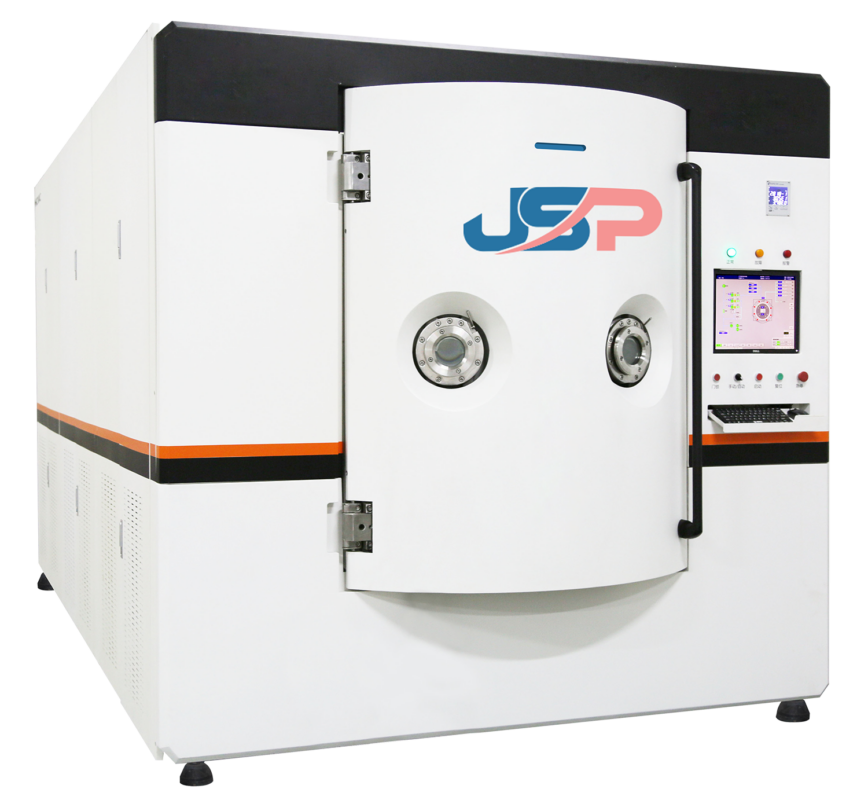
2. Sputter Deposition Two types of sputter deposition are currently used in manufacturing applications:
ion beam sputtering and magnetron sputtering. In the former, an ion beam directs a high electric field toward the surface of the material to be vaporized. This causes the metal vapor gases to ionize after which momentum transfer directs those ions toward the target production part. In magnetron sputtering, positively charged ions are accelerated by an electrical field and then superimposed onto the target parts. This process is commonly used in the medical industry for manufacturing lab products and optical films.
3. Arc Vapor Deposition (PVD coating) method at Bend Plating is arc vapor deposition
This process uses a low-voltage arc to evaporate metal source material into vaporized metal particles. These evaporated metal atoms combine with reactive gas molecules in a plasma state that once again condense on relatively cooler production parts in close proximity. Production parts spin on a multi-axis rack carousel to produce an evenly distributed lifetime coating in colors that include hues of black, bronze, gold, graphite, nickel, blue, purple, and “rainbow” combinations of more than one color. It is the most environmentally friendly method, and it results in a very thin (0.25 to 4.0 microns) hard metallic coating that is available in a wide variety of colors. PVD finish has a transparent quality that allows underlying chrome or polish to shine through.Matte and brushed metal finishes also receive PVD to lock in these desired physical appearances for a lifetime of corrosion, chemical, and scratch resistance.PVD can also be used on lower-cost or lighter weight base materials (including plastic and aluminum) and provide superior aesthetic looks, abrasion, and corrosion resistance.
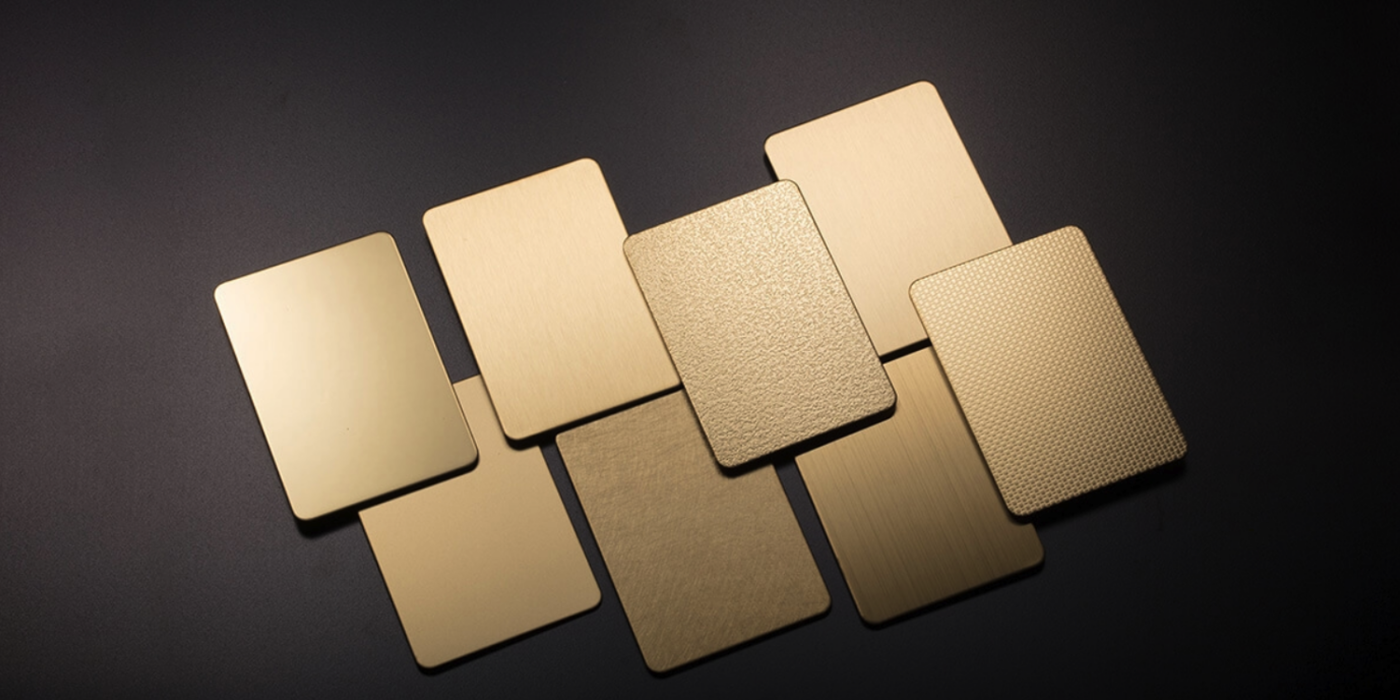
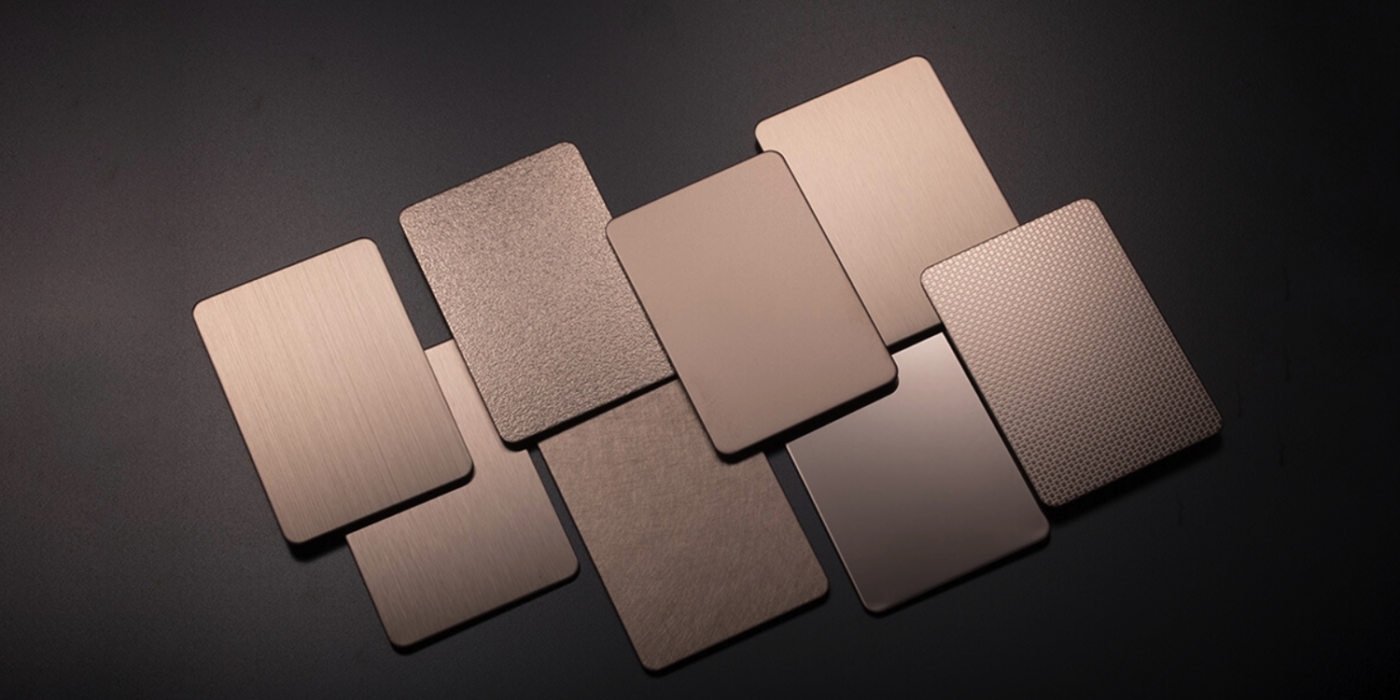
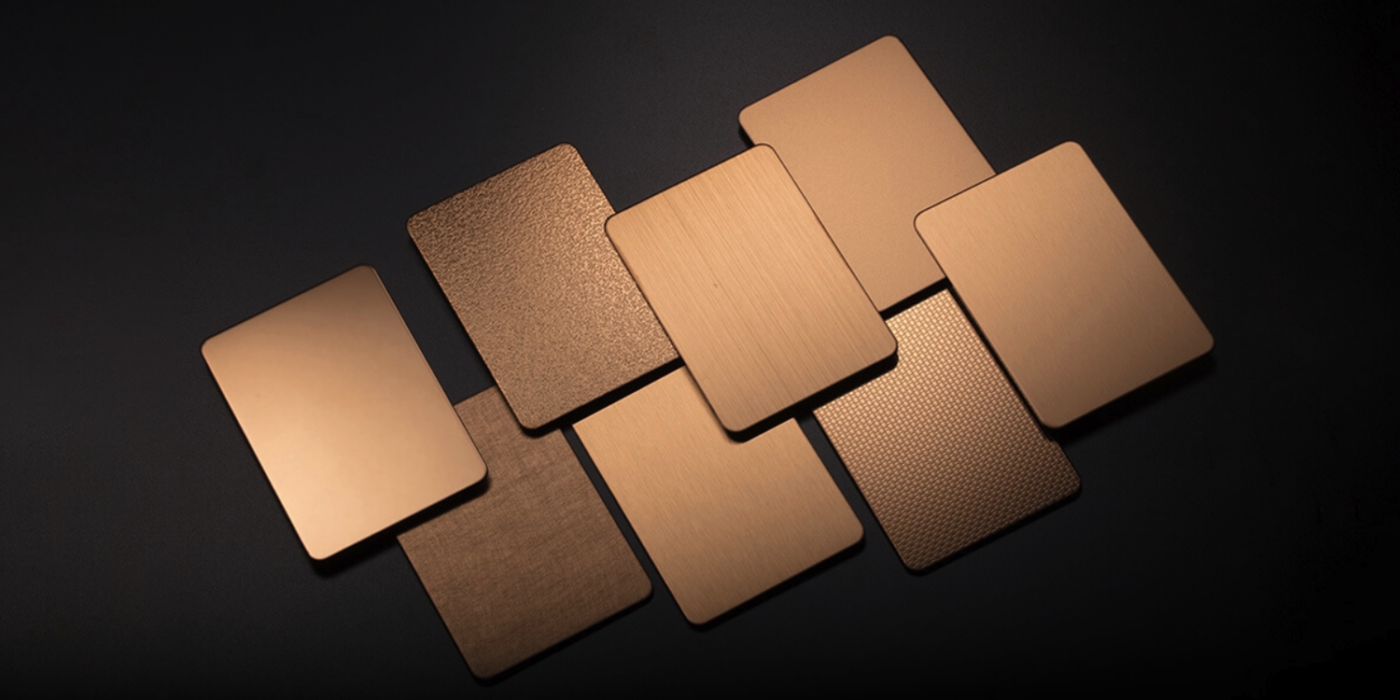
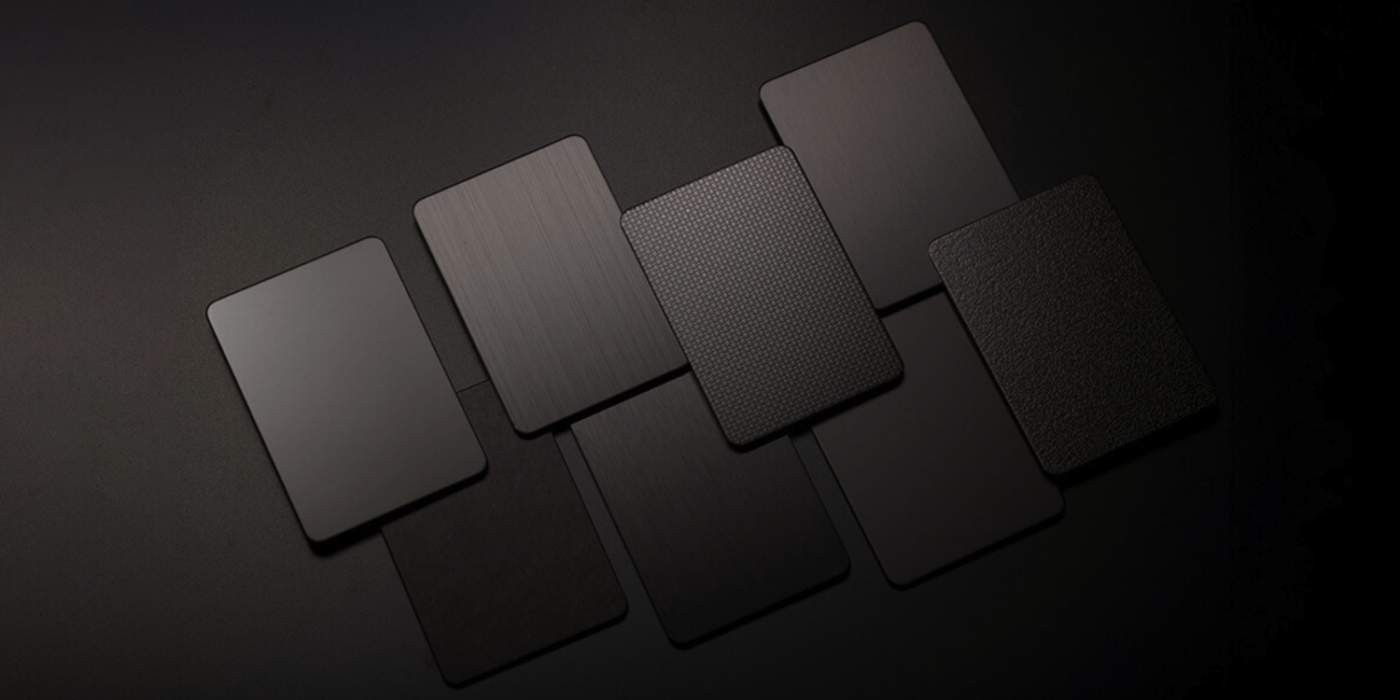